BioChemicals/Renewable ChemicalsBioRefineries/Renewable Fuel ProductionBiorefinery/Fuel Production InfrastructureCo-ProductsEnvironmental Protection AgencyFederal Agency/Executive BranchFeedstocksGreen JobsHistory of Advanced BiofuelsInfrastructureLouisianaMarketing/Market Forces and SalesNot AgricultureOriginal Writing, Opinions Advanced Biofuels USAProcessR & D FocusSmall scale biorefineriesSustainability
September 23, 2014
by Joanne Ivancic* (Advanced Biofuels USA) Golden Leaf Energy’s Troy A. Clark grew up in Louisiana. Studying chemical engineering at Tulane University brought him into contact with the oil industry. And yet, as his career progressed, he was drawn to renewables. Initially working as a dispatcher of ethanol for fuel, he forged relationships with companies from New Orleans to Detroit, then explored building a cellulosic ethanol biorefinery using sugar cane bagasse. Eventually, coming full circle, his company transitioned from using restaurant brown trap grease to manufacture biodiesel along the West Bank’s Harvey Canal to producing high tech bio-based lubricants for the oil industry from the same "funky mess," as Clark describes it.
His journey embodies a dynamic evident throughout the advanced biofuels industry.
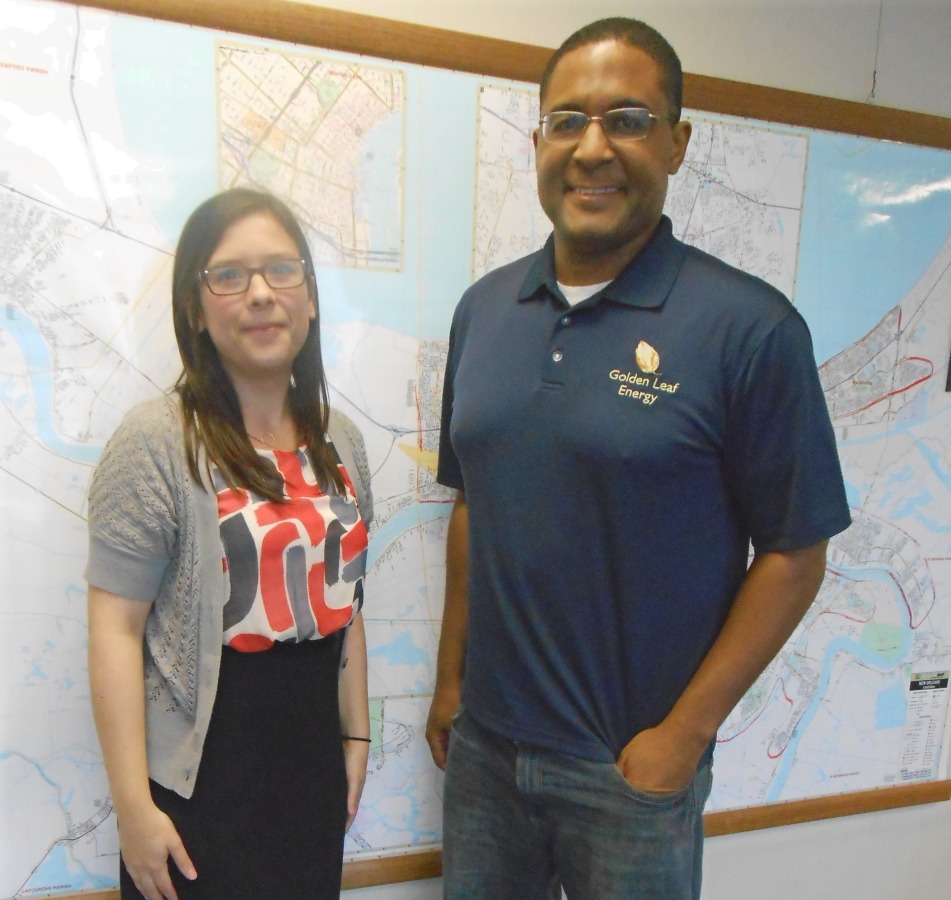
Sadly for those who would like to see a speedy transition away from use of fossil fuels for transportation purposes, Clark’s story from oil industry to renewables and back to the oil industry reflects a not uncommon theme in the renewable fuels sector. California’s Origin Oil followed a similar path with its algae-based lubricants marketed to the gas and oil fracking market. And New Zealand’s Lanza Tech has taken a biogas fermentation-to-ethanol technology to China where smokestacks at steel mills feed the gas to the biological process. Jim Lane of Biofuels Digest calls this merger of “green” bio-based feedstocks or technologies with “black” fossil fuel enterprises, the Olive Economy.
Clark is not giving up entirely on hope for bio-based fuels and materials to someday displace petroleum; but, he says, “The transportation fuel system that we have works; it’s hard to get people off it. It really is.”
He understands that from not only personal observation, but from participating in the markets as a consumer, dispatcher and entrepreneur.
From Dispatcher to Producer; Not without Set-Backs
Clark started as distributor of ethanol in the mid-west. He matched product from smaller ethanol producers such as DART Disposal and Recycling Technologies, Inc. who fermented waste soda, beer, wine, pharmaceuticals, candy, mouthwash and such into ethanol; with buyers in the transportation fuels business.
But Clark wanted to do more. He wanted to make something. With partner Dr. Calvin Mackie and the Louisiana State University’s Audubon Sugar Institute, they explored making cellulosic ethanol from sugar cane bagasse. At the time, they got stymied by the same biomass recalcitrance that has plagued other efforts and directed their attention to developing biodiesel refineries instead because they were relatively easy to build.
“We had a novel concept of a small facility that was modular and could take in any kind of feedstock,” Clark explains. They built a prototype facility in Harvey, Louisiana, using proprietary innovations that they developed to use brown grease, what Clark calls, “the bottom of the barrel” for biodiesel feedstock. Because their process could efficiently convert high levels (up to 90%) of free fatty acids (FFAs), what Clark calls “the enemy” of efficient biodiesel production, Golden Leaf Energy was able to hold down feedstock costs.
“We love FFAs because we know the more FFAs there are, the cheaper the product/feedstock is going to be. And because our facility is designed to take in up to 90% FFAs, we have no problem with that,” says Clark. FFAs have to go through a couple of chemical processes to convert it for use in the biodiesel process.
Again, typically for many innovations in the biofuels industry, key processes and “secret sauce” recipes are held close to the vest. “There’s some technology there; in our case it is cutting edge technology. For us, we don’t talk about it. It’s just a black box; it’s just magic. We process it and take it all the way through after that,” is all Clark will say about Golden Leaf Energy’s proprietary conversion of the FFAs.
Eventually, however, also typical of many in this business, even that processing innovation wasn’t enough to overcome the low margins and policy uncertainty of the biodiesel industry particularly the on-again, off-again federal biodiesel production tax incentive and the threat to the value of Renewable Fuel Standard RINs posed by the Environmental Protection Agency’s proposed downward adjustment to renewable volume obligations for the US transportation fuel market. Clark notes that most biodiesel is consumed as blendstock for diesel by the oil industry to comply with federal regulations, and to reap the RINs financial incentive. “They play largely a RIN game; so their consumption of biodiesel is almost entirely because of the RIN issue, because they are obligated to use it.”
Considering these uncertainties, Clark says, “We found it (producing biodiesel) to be a bit of a challenge because the margins are low and it is almost completely dependent on whether or not the tax credit is in place. The companies that supply the raw materials have a lot of control over margins and have a lot of control over the marketplace in general.”
To limit feedstock expense, Golden Leaf Energy developed its own collection system with about 100 restaurants. It wasn’t enough product for their entire production, but enough to reduce the overall cost of feedstock while they were making biodiesel for the transportation market.
“I’m lucky,” Clark says. “I get to use brown grease, the bottom of the barrel. Most people can’t use brown grease because their facility is not set up to manage it. Brown grease is almost completely FFA. You are talking 75-80% FFA. Most facilities don’t have the pretreatment capabilities to manage it. We wanted to use brown grease from the beginning, so we developed pretreatment capabilities that allow us to use it.”
Clark insists that there is a lot of opportunity to sell biodiesel in the region from New Orleans to Houston. “You have about 43 % of the country’s refining capacity,” he explains. He believes that when the economics are right, there’s a vast market.
From Biofuels to Bioproducts
For now, Golden Leaf Energy is taking a different tack.
“That market (transportation fuels) is not as attractive to us. We had a small facility and because we were engineers and scientists, we felt we could do some more interesting things so we began to look for opportunities to use methyl ester in other chemistries. We rarely even call it biodiesel. We call it methyl ester because for us it is a chemical.
“And that chemical has certain advantages. It is an excellent solvent. What does that mean? What is a solvent? It can serve as a base for a bunch of other stuff. You can mix methyl ester with a lot of things. It combines well which means you can direct the chemistry toward solving various problems. And we’ve been able to direct it to solve the problem of lubricating metal-to-metal surfaces.
“Our lubricant has a lot of biodiesel in it, a lot of methyl ester in it. We aren’t the only guys on the block using biodiesel in that capacity. There are quite a few companies out there using it, but they don’t make/manufacture biodiesel the way we do; they don’t understand the product as well as we do. They typically buy it. But the opportunity for methyl ester to be used in any number of applications is through the roof. And that’s what we are most excited about.”
As is also typical in the advanced biofuels and bioproducts space these days, Golden Leaf Energy has a patent on the recipe for the lubricant; but not a patent on the process for converting feedstock with high proportions of FFAs. That information is too valuable to share with the world in a patent application. Like many in this game, Golden Leaf Energy keeps that close to the vest.
Innovation and More Innovation
“What’s next for us are the opportunities for using methyl ester as a base for future products, future chemicals. We’ll probably make some hydraulic fluids, more lubricants. We’re going to make lubricants that are used in traditional metal working environments, metal shops, maybe big industrial places.
“We think that our next product will be a slideway oil. Slideways are inside metal making machines with a lot of metal-to-metal contact--big surface areas with metal-to-metal contact. Methyl esters are very good in that environment. For us, the sky’s the limit in terms of opportunities for using methyl ester based chemistries for varied applications.”
Do customers care about being “green?”
Clark explains, “Yes, it matters to oil companies because they have to improve their narratives. If you can provide an improvement to the narrative combined with product performance at cost, at what they are paying, you’ll get the sale every time.
“I think ultimately, that has to be the focus of anybody in this space. That you are dealing with an entrenched product, petroleum. And when you start pulling back, you start to understand how far out petroleum products go, you’re seeing, one, how successful it is; but, two, you also see all these opportunities.
“What can we develop to displace those products? What can we develop to compete with those products? And if you can come up with chemistries that perform, and you aren’t too, too much more expensive, you have a legitimate opportunity to compete.
“Think about it from this standpoint. You are talking about some of the richest guys on the planet. They have absolutely no motivation to change. Because, ‘I’ve already won. I’ve got the most money.’ Not only is it not broke, it’s not broke by a mile as far as we’re concerned.
“And then they are getting better at what they do. They are getting better at finding oil and extracting oil.”
Petroleum Industry Psychology
Growing up in Louisiana with the prominent oil/gas/chemical industry enabled Clark to understand the psychology of this sector, to get a feel for what is important to this customer base.
“Where do they make their money?” he asks, as an introduction to sharing his take on his role in the oil industry and a key to his business model. “What they are most concerned about is pulling it out of the ground and that’s where I interact with them. And that’s where they spend the most money. ”
From conversations with oil executives, he says, he understands their priorities, “How efficiently and how successfully are (they) pulling oil out of the ground?” Clark’s lubricants serve this effort. And, his experience, similar to that of OriginOil’s, indicates that if he can compete with petroleum lubricants on price and performance, he can successfully compete.
With regard to any interest in transitioning from a petroleum-based world to a bio-based one, he emphasizes, “The scientists and engineers and businessmen in the world have to say we need to develop a renewable product that competes with petroleum products on price and performance. If you can’t do that, then there is no way, there is no incentive to do anything different.
“So our model, what we are here to do is to compete with these products on price and performance.
“And when we do that, there’s no objection: ‘Now you are on the list with everybody else and you’re just like everybody else: hey, give me a call. Your stuff worked for me.’”
Focus on Specialty Markets Provide Opportunity for Small Business
Founded in 2008, and still a start-up like many in this space, Golden Leaf Energy employs six people with four in production. Clark anticipates hiring as they grow, adding a weekend and a third shift. For every additional shift they will add two people. As they expand into other products, he expects to add capacity to their existing 2.2 MMgy facility and that will mean more hires.
They are actively developing new products. Clark repeats the word, “innovation.” "We have some interesting partnerships going. We are just cranking up this partnership with Kraev (Laboratories),” he explains, introducing Dr. Kevin Roberson. “He’s a scientist; we’re just contracting out brains, contracting out brain power," he joked. "We are going to continue to do that (instead of hiring scientists at this time).”
Troy Clark has met each bump in the advanced biofuels road with persistence, belief in the potential of this sector and trust in thoughtful innovation. Despite the deviations from a direct path to renewable fuels, Clark is encouraging, “Smart people who’ve got ideas, if they want to make a home in the alternative fuels space, there’s a lot of opportunity.”
*Joanne Ivancic, serves as Executive Director of Advanced Biofuels USA. She also served as a lobbyist promoting advanced biofuels research and production on Capitol Hill and with executive agencies. She has observed the development of advanced biofuels’ research and financing for more than fifteen years. From 2010 to 2013 she was voted one of the Top 100 People in Bioenergy by Biofuels Digest readers and editors.
This article is part of a series of articles looking behind the scenes at the people, places and projects that contribute pieces of the story of the development of advanced biofuels and the bio-based economy in the early 21st century.
Tags
Share
Nearly 55,000 articles in our online library!
Use the categories and tags listed below to access the nearly 50,000 articles indexed on this website.
Advanced Biofuels USA Policy Statements and Handouts!
- For Kids: Carbon Cycle Puzzle Page
- Why Ethanol? Why E85?
- Just A Minute 3-5 Minute Educational Videos
- 30/30 Online Presentations
- “Disappearing” Carbon Tax for Non-Renewable Fuels
- What’s the Difference between Biodiesel and Renewable (Green) Diesel? 2020 revision
- How to De-Fossilize Your Fleet: Suggestions for Fleet Managers Working on Sustainability Programs
- New Engine Technologies Could Produce Similar Mileage for All Ethanol Fuel Mixtures
- Action Plan for a Sustainable Advanced Biofuel Economy
- The Interaction of the Clean Air Act, California’s CAA Waiver, Corporate Average Fuel Economy Standards, Renewable Fuel Standards and California’s Low Carbon Fuel Standard
- Latest Data on Fuel Mileage and GHG Benefits of E30
- What Can I Do?
Donate
DonateARCHIVES
- July 2025
- June 2025
- May 2025
- April 2025
- March 2025
- February 2025
- January 2025
- December 2024
- November 2024
- October 2024
- September 2024
- August 2024
- July 2024
- June 2024
- May 2024
- April 2024
- March 2024
- February 2024
- January 2024
- December 2023
- November 2023
- October 2023
- September 2023
- August 2023
- July 2023
- June 2023
- May 2023
- April 2023
- March 2023
- February 2023
- January 2023
- December 2022
- November 2022
- October 2022
- September 2022
- August 2022
- July 2022
- June 2022
- May 2022
- April 2022
- March 2022
- February 2022
- January 2022
- December 2021
- November 2021
- October 2021
- September 2021
- August 2021
- July 2021
- June 2021
- May 2021
- April 2021
- March 2021
- February 2021
- January 2021
- December 2020
- November 2020
- October 2020
- September 2020
- August 2020
- July 2020
- June 2020
- May 2020
- April 2020
- March 2020
- February 2020
- January 2020
- December 2019
- November 2019
- October 2019
- September 2019
- August 2019
- July 2019
- June 2019
- May 2019
- April 2019
- March 2019
- February 2019
- January 2019
- December 2018
- November 2018
- October 2018
- September 2018
- August 2018
- July 2018
- June 2018
- May 2018
- April 2018
- March 2018
- February 2018
- January 2018
- December 2017
- November 2017
- October 2017
- September 2017
- August 2017
- July 2017
- June 2017
- May 2017
- April 2017
- March 2017
- February 2017
- January 2017
- December 2016
- November 2016
- October 2016
- September 2016
- August 2016
- July 2016
- June 2016
- May 2016
- April 2016
- March 2016
- February 2016
- January 2016
- December 2015
- November 2015
- October 2015
- September 2015
- August 2015
- July 2015
- June 2015
- May 2015
- April 2015
- March 2015
- February 2015
- January 2015
- December 2014
- November 2014
- October 2014
- September 2014
- August 2014
- July 2014
- June 2014
- May 2014
- April 2014
- March 2014
- February 2014
- January 2014
- December 2013
- November 2013
- October 2013
- September 2013
- August 2013
- July 2013
- June 2013
- May 2013
- April 2013
- March 2013
- February 2013
- January 2013
- December 2012
- November 2012
- October 2012
- September 2012
- August 2012
- July 2012
- June 2012
- May 2012
- April 2012
- March 2012
- February 2012
- January 2012
- December 2011
- November 2011
- October 2011
- September 2011
- August 2011
- July 2011
- June 2011
- May 2011
- April 2011
- March 2011
- February 2011
- January 2011
- December 2010
- November 2010
- October 2010
- September 2010
- August 2010
- July 2010
- June 2010
- May 2010
- April 2010
- March 2010
- February 2010
- January 2010
- December 2009
- November 2009
- October 2009
- September 2009
- August 2009
- July 2009
- June 2009
- May 2009
- April 2009
- March 2009
- February 2009
- January 2009
- December 2008
- November 2008
- October 2008
- September 2008
- August 2008
- July 2008
- June 2008
- May 2008
- April 2008
- March 2008
- February 2008
- January 2008
- December 2007
- November 2007
- October 2007
- September 2007
- August 2007
- June 2007
- February 2007
- January 2007
- October 2006
- April 2006
- January 2006
- April 2005
- December 2004
- November 2004
- December 1987
CATEGORIES
- About Us
- Advanced Biofuels Call to Action
- Aviation Fuel/Sustainable Aviation Fuel (SAF)
- BioChemicals/Renewable Chemicals
- BioRefineries/Renewable Fuel Production
- Business News/Analysis
- Cooking Fuel
- Education
- 30/30 Online Presentations
- Competitions, Contests
- Earth Day 2021
- Earth Day 2022
- Earth Day 2023
- Earth Day 2024
- Earth Day 2025
- Executive Training
- Featured Study Programs
- Instagram TikTok Short Videos
- Internships
- Just a Minute
- K-12 Activities
- Mechanics training
- Online Courses
- Podcasts
- Scholarships/Fellowships
- Teacher Resources
- Technical Training
- Technician Training
- University/College Programs
- Events
- Coming Events
- Completed Events
- More Coming Events
- Requests for Speakers, Presentations, Posters
- Requests for Speakers, Presentations, Posters Completed
- Webinars/Online
- Webinars/Online Completed; often available on-demand
- Federal Agency/Executive Branch
- Agency for International Development (USAID)
- Agriculture (USDA)
- Commerce Department
- Commodity Futures Trading Commission
- Congressional Budget Office
- Defense (DOD)
- Air Force
- Army
- DARPA (Defense Advance Research Projects Agency)
- Defense Logistics Agency
- Marines
- Navy
- Education Department
- Energy (DOE)
- Environmental Protection Agency
- Federal Energy Regulatory Commission (FERC)
- Federal Reserve System
- Federal Trade Commission
- Food and Drug Administration
- General Services Administration
- Government Accountability Office (GAO)
- Health and Human Services (HHS)
- Homeland Security
- Housing and Urban Development (HUD)
- Interior Department
- International Trade Commission
- Joint Office of Energy and Transportation
- Justice (DOJ)
- Labor Department
- National Academies of Sciences Engineering Medicine
- National Aeronautics and Space Administration
- National Oceanic and Atmospheric Administration
- National Research Council
- National Science Foundation
- National Transportation Safety Board (NTSB)
- Occupational Safety and Health Administration
- Overseas Private Investment Corporation
- Patent and Trademark Office
- Securities and Exchange Commission
- State Department
- Surface Transportation Board
- Transportation (DOT)
- Federal Aviation Administration
- National Highway Traffic Safety Administration (NHTSA)
- Pipeline and Hazardous Materials Safety Admin (PHMSA)
- Treasury Department
- U.S. Trade Representative (USTR)
- White House
- Federal Legislation
- Federal Litigation
- Federal Regulation
- Feedstocks
- Agriculture/Food Processing Residues nonfield crop
- Alcohol/Ethanol/Isobutanol
- Algae/Other Aquatic Organisms/Seaweed
- Atmosphere
- Carbon Dioxide (CO2)
- Field/Orchard/Plantation Crops/Residues
- Forestry/Wood/Residues/Waste
- hydrogen
- Manure
- Methane/Biogas
- methanol/bio-/renewable methanol
- Not Agriculture
- RFNBO (Renewable Fuels of Non-Biological Origin)
- Seawater
- Sugars
- water
- Funding/Financing/Investing
- grants
- Green Jobs
- Green Racing
- Health Concerns/Benefits
- Heating Oil/Fuel
- History of Advanced Biofuels
- Infrastructure
- Aggregation
- Biofuels Engine Design
- Biorefinery/Fuel Production Infrastructure
- Carbon Capture/Storage/Use
- certification
- Deliver Dispense
- Farming/Growing
- Precursors/Biointermediates
- Preprocessing
- Pretreatment
- Terminals Transport Pipelines
- International
- Abu Dhabi
- Afghanistan
- Africa
- Albania
- Algeria
- Angola
- Antarctica
- Arctic
- Argentina
- Armenia
- Aruba
- Asia
- Asia Pacific
- Australia
- Austria
- Azerbaijan
- Bahamas
- Bahrain
- Bangladesh
- Barbados
- Belarus
- Belgium
- Belize
- Benin
- Bermuda
- Bhutan
- Bolivia
- Bosnia and Herzegovina
- Botswana
- Brazil
- Brunei
- Bulgaria
- Burkina Faso
- Burundi
- Cambodia
- Cameroon
- Canada
- Caribbean
- Central African Republic
- Central America
- Chad
- Chile
- China
- Colombia
- Congo
- Congo, Democratic Republic of
- Costa Rica
- Croatia
- Cuba
- Cyprus
- Czech Republic
- Denmark
- Dominican Republic
- Dubai
- Ecuador
- El Salvador
- Equatorial Guinea
- Eqypt
- Estonia
- Eswatini/Swaziland
- Ethiopia
- European Union (EU)
- Fiji
- Finland
- France
- French Guiana
- Gabon
- Georgia
- Germany
- Ghana
- Global South
- Greece
- Greenland
- Grenada
- Guatemala
- Guinea
- Guyana
- Haiti
- Honduras
- Hong Kong
- Hungary
- Iceland
- India
- Indonesia
- Iran
- Iraq
- Ireland
- Israel
- Italy
- Ivory Coast
- Jamaica
- Japan
- Jersey
- Jordan
- Kazakhstan
- Kenya
- Korea
- Kosovo
- Kuwait
- Laos
- Latin America
- Latvia
- Lebanon
- Liberia
- Lithuania
- Luxembourg
- Macedonia
- Madagascar
- Malawi
- Malaysia
- Maldives
- Mali
- Malta
- Marshall Islands
- Mauritania
- Mauritius
- Mexico
- Middle East
- Moldova
- Monaco
- Mongolia
- Morocco
- Mozambique
- Myanmar/Burma
- Namibia
- Nepal
- Netherlands
- New Guinea
- New Zealand
- Nicaragua
- Niger
- Nigeria
- North Africa
- North America
- North Korea
- Northern Ireland
- Norway
- Oman
- Pakistan
- Panama
- Papua New Guinea
- Paraguay
- Peru
- Philippines
- Poland
- Portugal
- Qatar
- Republic of
- Romania
- Russia
- Rwanda
- Saudi Arabia
- Scotland
- Senegal
- Serbia
- Sierra Leone
- Singapore
- Slovakia
- Slovenia
- Solomon Islands
- South Africa
- South America
- South Korea
- South Sudan
- Southeast Asia
- Spain
- Sri Lanka
- Sudan
- Suriname
- Sweden
- Switzerland
- Taiwan
- Tanzania
- Thailand
- Timor-Leste
- Togo
- Trinidad and Tobago
- Tunisia
- Turkey
- Uganda
- UK (United Kingdom)
- Ukraine
- United Arab Emirates UAE
- Uruguay
- Uzbekistan
- Vatican
- Venezuela
- Vietnam
- Wales
- Zambia
- Zanzibar
- Zimbabwe
- Marine/Boat Bio and Renewable Fuel/MGO/MDO/SMF
- Marketing/Market Forces and Sales
- Opinions
- Organizations
- Original Writing, Opinions Advanced Biofuels USA
- Policy
- Presentations
- Biofuels Digest Conferences
- DOE Conferences
- Bioeconomy 2017
- Bioenergy2015
- Biomass2008
- Biomass2009
- Biomass2010
- Biomass2011
- Biomass2012
- Biomass2013
- Biomass2014
- DOE Project Peer Review
- Other Conferences/Events
- R & D Focus
- Carbon Capture/Storage/Use
- Co-Products
- Feedstock
- Logistics
- Performance
- Process
- Vehicle/Engine/Motor/Aircraft/Boiler
- Yeast
- Railroad/Train/Locomotive Fuel
- Resources
- Books Web Sites etc
- Business
- Definition of Advanced Biofuels
- Find Stuff
- Government Resources
- Scientific Resources
- Technical Resources
- Tools/Decision-Making
- Rocket/Missile Fuel
- Sponsors
- States
- Alabama
- Alaska
- Arizona
- Arkansas
- California
- Colorado
- Connecticut
- Delaware
- Florida
- Georgia
- Hawai'i
- Idaho
- Illinois
- Indiana
- Iowa
- Kansas
- Kentucky
- Louisiana
- Maine
- Maryland
- Massachusetts
- Michigan
- Midwest
- Minnesota
- Mississippi
- Missouri
- Montana
- Native American tribal nation lands
- Nebraska
- Nevada
- New Hampshire
- New Jersey
- New Mexico
- New York
- North Carolina
- North Dakota
- Ohio
- Oklahoma
- Oregon
- Pennsylvania
- Puerto Rico
- Rhode Island
- South Carolina
- South Dakota
- Tennessee
- Texas
- Utah
- Vermont
- Virginia
- Washington
- Washington DC
- West Coast
- West Virginia
- Wisconsin
- Wyoming
- Sustainability
- Uncategorized
- What You Can Do
tags
Advanced Clean Fleets Rule
100 octane
100% SAF (Sustainable Aviation Fuel)
103 octane
105 octane
108 octane
109 octane
110 octane
113 octane
119 octane
2016 US House and Senate Campaigns
2016 US Presidential Campaign
2018 US Senate and House Campaigns Other Election Activities
2020 Election
2022 Election
2022 US Senate and House Campaign
2024 Election
2nd generation biofuels
3-D
3D printing
3rd generation biofuels
4-H
40A Biodiesel and Renewable Diesel Tax Incentive
40B Sustainable Aviation Fuel Tax Credit
45Q Carbon Oxide Sequestration Tax Credit
45V Hydrogen Production Tax Credit
45X Advanced Manufacturing Production Tax Credit
45Z Clean Fuel Production Tax Credit
48C Advanced Energy Project Tax Credit
4th generation fuels
7% solution
81 Octane
84 octane
85 octane
87 octane
88 octane
89 octane
90 octane
91 octane
92 octane
93 octane
94 octane
95 octane
96 octane
98 octane
A20 (20% methanol/bioethanol)
abatement
abu
Abu Dhabi
acacia
acetate
acetic acid
acetone
acid
acid hydrolysis
adaptive evolution
additional carbon
additionality
adequate/inadequate domestic supply
Administrative Procedure Act
adsorption
Advanced Biofuel Payment Program
advanced biofuel prices
Advanced biofuels
advanced biofuels production
Advanced Clean Cars II Rule (ACC and ACCII)
Advanced Clean Trucks Rule
advanced ethanol
advanced ethanol tax credit
advertising campaign
aerobic digestion
aerosols
Affordable Clean Energy Program (ACE)
afforestation
Afghanistan
Africa
AGARDA (Agriculture Advanced Research and Development Authority)
agave
aggregation
Agricultural Conservation Easement Program (ACEP)
agricultural economics
Agricultural Policy
Agricultural waste/residue
Agriculture
agrivoltaic/agrovoltaic
agroforestry
agrofuels
agronomy
Air Force
air pollution control
Air Pollution Policy
air quality
Aircraft engine emissions
airports
Alabama
Alaska
Albania
albedo
Alberta
albizia
alcohol fuel cells
alcohol fuels
alcohol-to-diesel
alcohol-to-jet (ATJ)/ethanol-to-jet (ETJ)
alfalfa
algae
algae contamination
algae cultivation
algae extraction
algae harvesting
algae parity
algae separation
algal biofuels
Algeria
Algiers
alkaline exchange membrane (AEM)
alkanes
alkenes
alkylate
alligator fat
almond
almond hulls shells
alternative energy vehicles
alternative fuels
Alternative Fuels Credit
alternative fuels excise tax credit
Alternative Fuels Tax Credit (AFTC)
aluminum
Amazon
American Le Mans Series (ALMS)
ammonia
ammonia fiber explosion (AFEX)
ammonia fuel cell
ammonia price
ammonia terminal
amylose
anaerobic digestate
anaerobic digester/digestion
and Energy Use in Transportation Model
Angola
anhydrous ethanol
animal bedding
animal fat
animal feed
animal waste
Antactica
Antarctica
antibiotics
antitrust
apple
Appropriations
APR (Aqueous Phase Reforming)
aquaculture
aquatic organisms
Arabidopsis
arabinose
ARCA
Archaea
Architecture
Arctic
Argentian
Argentiina
Argentina
Arizona
Arkansas
Armenia
Army Corps of Engineers
aromatics
aromatics price
ARPA-C
ARPA-E
ARPA-Terra
arrandi
artificial intelligence
Aruba
Asia
Asia Pacific
asphalt/bitumen
ASTM
ASTM 6866
ASTM D1655
ASTM D2880
ASTM D396
ASTM D4054
ASTM D4806 Denatured fuel ethanol
ASTM D4814
ASTM D5798
ASTM D6751
ASTM D7467 (B6-B20)
ASTM D7544
ASTM D7566 (Standard Specification for Aviation Turbine Fuel Containing Synthesized Hydrocarbons)
ASTM D7862
ASTM D7875
ASTM D7901 (DME-Dimethyl Ether for Fuel Purposes)
ASTM D8076
ASTM D8181
ASTM D975
ASTM E3050 Denatured Ethanol for Cooking
ASTM E3146
ASTM standards
ASTM WK55232 (D02)
ASTM WK63392
ATJ-SPK (Alcohol to Jet Synthetic Paraffinic Kerosene)
Atlantic Canada
atmosphere
Atomic Energy Commission (AEC)
Australia
Australian pine
Austria
Auto manufacturer
automotive
aviation
aviation fuel (SAF) benefits
aviation fuel (SAF) mandates
aviation fuel (SAF) price
aviation fuel (SAF) production
aviation fuel (SAF) pumps/delivery
aviation fuel (SAF) tax credit
aviation fuel (SAF) terminal
Aviation Fuel/Sustainable Aviation Fuel (SAF)
Aviation Gasoline/AvGas
avocado
award
awards/recognition
Azerbaijan.
b
B0
B10
B100
B100 pumps
B11
B12
B12.5
B13
B14
B15
B16
B17
B19
B2
B20
B24
B25
B3
B30
B30RD10
B33
B35
B4
B40
B49
B5
B50
B50RD50
B6
B60
B7
B70
B75
B8
B80
B98
B99
Babados nut tree
babassu
bacteria
bagasse
Bahamas
Bahrain
bamboo
banana
banana stems
Bangladesh
bankruptcy
Barbados
barge
barley
barley fiber
barley protein
barley straw
Basque
batteries
Battery Electric Vehicles (BEV)
bauxite
beauty leaf tree
beaver
beer
bees
Belarus
Belgium
Belize
Benin
benzene
Bermuda
Bhutan
big bluestem
big data
Big Food
Big Oil/Oil Majors
BIGoil
billion ton study
bio
Bio LPG (Bio Liquid Petroleum Gas)
bio-based diesel benefits
bio-based economy
Bio-CNG pumps
Bio-CNG/RNG terminal
bio-LNG (Liquified Natural Gas)
Bio-LNG Pumps (Liquified Natural Gas)
Bio-LNG terminal
bio-natural gas
bio-NGV (natural gas for vehicles)
bio-oil/pyrolysis oil
bio-SPK (bio derived synthetic paraffinic kerosene)
biobased
Biobased Market Access and Development Grants
Biobased Markets Program
biobased materials
Biobased Product Manufacturing Assistance Program
biochar
biochemical conversion
BioChemicals/Renewable Chemicals
biociiesel
bioconversion
Biocrude/Green Crude/SynCrude
biodegradable
biodiesel
biodiesel blend wall
biodiesel EN 14214
Biodiesel Fuel Education Program
biodiesel pipeline
biodiesel prices
biodiesel production
biodiesel pumps
biodiesel quality
biodiesel standards
biodiesel tax credit
biodiesel technologies
biodiesel terminal
biodiversity
bioeconomy
bioelectricity
bioelectrochemical conversion
bioenergy
Bioenergy Program for Advanced Biofuels
Bioenergy with Carbon Capture and Storage (BECCS)
biofoundry
Biofuel
biofuel cells
biofuel consumption
Biofuel Crops
biofuel distribution
Biofuel Infrastructure Partnership (BIP)
biofuel producer tax credit
biofuel production
biofuel tax credit
biofuel terminal
Biofuels Directive
biofuels education
Biogas
Biogas pipeline
Biogasoline/Renewable Gasoline
Biogasoline/Renewable Gasoline pumps
biogenic carbon
biogenic emissions
Bioheat
biohydrocarbons
biohydrogen
BioIsoprene
BioMADE
biomanufacturing
biomass
Biomass Carbon Removal and Storage (BiCRS)
Biomass Crop Assistance Program (BCAP)
biomass hydrolysis
biomass recalcitrance
Biomass Research and Development initiative (BRDI)
biomass sorghum
Biomass to Liquid (BTL)
biomass transportation
biomaterials
bioplastics
biopower
BioPreferred
bioproducts
biopropene
bioprospecting
BioRefineries/Renewable Fuel Production
Biorefinery Assistance Program (BAP) old 9003
Biorefinery Renewable Chemical Biobased Product Mfgr Assistance 9003 Program
BioRenewable-1 (BR-1)
BioSNG
Biotechnology
birch
bitter orange
black carbon
black grease
black liquor
black locust
black soldier fly
Blend wall
blender
blender pumps
Blenders Credit
blending
blendstock
blockchain
blue carbon
boat fuel
boiler/furnace fuel
Bolivia
bolt-on
Bonaire
bonds
book-and-claim
border tax
Borneo
Bosnia and Herzegovina
Botswana
BQ-9000
Brachiaria
bracken
brackish water
brash
Brassica
Brazil
breadfruit/ulu
breweries
brine
British Columbia
broker
brown grease
brownfields
Brunei
Btu's
BTX (Benzene Toluene Xylene)
Bu12.5
Bu16
Budget
building block chemicals
Bulgaria
bunker
bunker oil
Bureau of Land Management (BLM)
Burkina Faso
Burma
Burundi
buses
Business and Industry Program (B&I)
business law
business resources
Business/General Aviation
butadiene
butandeiol (bio-BDO)
Butane
butanediol
butanol emissions
butanol/biobutanol
butyl acetate
butylene
butyric acid
by
c
C1
C2
C21
C3 sugar
C4 grasses
C5 sugar
C6 sugar
Cabo Verde
cactus
cactus pear
cagaita
calibration
California
California Air Resources Board (CARB)
Calophyllum hawthorn
Cambodia
Camelina
camels
Cameroon
Canad
Canada
Canary Islands
canary reed grass
canarygrass
candle nut
cannabis
canola straw
Canola/Rapeseed
cap-and-invest
cap-and-trade
capybara
capybras
carbohydrates
carbon
carbon capture and storage (CCS)
carbon capture and utilization (CCU)
carbon cost
carbon credit
carbon credit markets
carbon cycle
carbon debt
Carbon Dioxide (CO2)
carbon efficiency
carbon emissions
carbon fiber
carbon insets
Carbon Intensity (CI)/Carbon Footprint
carbon life cycle
carbon markets
Carbon Monoxide (CO)
carbon negative
carbon neutrality
carbon offsets
carbon pipeline
carbon price
carbon recycling
carbon removal
carbon sink
carbon standard
carbon tax
Carbon tax border adjustments
carbon tax-and-dividend
carbon terminal
carbon user fee
Carbon Utilization and Biogas Education Program
carbon-14 testing
carbon-efficient fuels
carbon/CO2 sequestration
carcinogens
cardoon
Caribbean
carinata
carinata/brassica carinata
carob
CAS Registry
cashew
cashew apple
Cashew Nut Shell Liquid (CNSL)
CASI
Cassava
cassava price
cassava pulp
cassava stalk
castor bean
castor stalk
catalysis
catalysts
catalytic decarboxylation
catalytic hydrothermal conversion
catalytic hydrothermal conversion-to-jet (CHCJ)
catalytic hydrothermal gasification
catalytic hydrothermolysis jet CHJ pathway
cattails
cattle
cavitation
CBD (cannabidiol)
CBG (compressed biogas)
cell culturing
cellulase enzymes
cellulose
cellulosic biofuel
Cellulosic biomass
cellulosic diesel
Cellulosic ethanol
cellulosic ethanol price
cellulosic feedstock
cellulosic production tax credit
cellulosic sugars
Cellulosic Tax Credit
cellulosic waiver credit
cement
Central African Republic
Central America
Certificate Program
Certificates of Origin (COs)
certification
certification fuels
cesium
cetane
Chad
change in soil condition
charging stations
CHCJ-5
chemical-looping hydrogen method
Chesapeake Bay
chicken feathers
chickens
Chile
Chili
China
chitin
chp
chromium
chufa/cyperus esculents/nutsedge
CIA
circular economy
citrus
citrus greening disease
Citrus Peel
clean air
Clean Air Act (CAA)
clean diesel
Clean Fuel Standard/Policy (CFS)
Clean Heat Standards
Clean Power Plan (CPP)
Clean Trucks Plan
Clean Water Act
climate change
Climate Change Adaptation
climate change effects
climate change mitigation
climate legislation
climate smart/modern/conservation agriculture
closed-loop system
Clostridium thermocellum
cloud point
clover
cmelina
CNG Conversion kit
co
co-generation
co-location
Co-op Extension
co-operative
co-processing
co-products
CO2 Electrolysis
CO2 neutral fuels
CO2Removal Certificates (CORCs)
coal
Coal and Biomass to Liquid (CBTL)
Coast Guard
coastal habitat conservation
coastal hay
cobalt
cock's foot
coco
coco methyl ester (CME)
cocoa
Coconut
coffee
coffee cherries
coffee grounds
coffee pulp
cold flow
cold-tolerance
college/university
Colombia
Colorado
combined heat and power (CHP)
Comment Request
commercial flights
commercialization
commissioning
commo
Commodity Credit Corporation (CCC)
Commodity Futures Trading Commission (CFTC)
commodity trading
common reed
Community activity
community college
Community involvement/engagement
community scale
Community Wood Energy Program
competition
compliance
compliance credits
compost
Compressed Natural Gas (CNG/R-CNG/bioCNG)
compression ratios
compression-ignition engine
computer simulation
concrete
condensate
Congo
Congressional Budget Office (CBO)
Congressional Review Act
Connecticut
Conservation Reserve Program (CRP)
Conservation Stewardship Program (CSP)
construction and demolition waste/debris
consumer education
contamination
contest
contrails
conversion technology
Cook Islands
cook stoves
cooking fuel
cooperatives
COP21
COP22
COP23
COP24
COP25
COP26
COP27
COP28
COP29
COP30
copper
coppice
cordgrass
corn bran
Corn cobs
corn ethanol
corn fiber
corn growers
corn harvest
corn kernel
corn meal
corn oil
corn oil/distillers corn oil (DCO)
corn prices
corn stalks
corn stover
corn supply
corn surplus
corn syrup
corn-based products
corn/maize
Corporate Average Fuel Economy (CAFE) standards
corporate social responsibility
corrosion
corruption
CORSIA (Carbon Offsetting and Reduction Scheme for International Aviation)
cosmetics
Costa Rica
cotton
cotton seed hulls
cotton seed oil
cotton stalk
cottonwood
Council on Environmental Quality
county
cover crops
cow rumen
cracking
Crambe
crassulacean acid metabolism plants (CAM)
crimes
criteria pollutants
Croatia
crop
crop insurance
cropland
croton
crowdfunding
crude lignin oil (CLO)
crude oil
Cruise Ships
Cuba
cup plant
cuphea
currency/foreign exchange policy
curriculum
cusi
Customs and Border Protection
cutworm caterpillars
cyanobacteria (blue-green algae)
cylindro
Cyprus
Czech Republic
d
D-3 (cellulosic) RINs
D-4 (bio-based diesel) RINs
d-5
D-5 (advanced biofuel) RINs
D-6 (renewable fuel) RINs
D-7 RINs (Cellulosic Diesel)
D-8 (proposed) RINs
D20 (20%DME)
D5 (5%DME)
dairy waste
dandelion
DARPA
date kernel oil
date palm
date palm pits
date palm waste
Dates
DDGS (distiller’s dried grains with solubles)
dead zone
decanol
decision-support tool
deep water drilling
Defense Logistics Agency (DLA)
Defense Production Act
deficit
definitions
deforestation
defossilization
Dehydration
Delaware
DeltaWing
demonstration
demonstration scale/unit
Denmark
densify
density
Department of Agriculture (USDA)
Department of Commerce
Department of Defense (DOD)
Department of Education
Department of Energy (DOE)
Department of Health and Human Services
Department of Homeland Security
Department of Justice
Department of Labor
Department of the Interior
Department of Transportation (DOT)
depolymerization
depots
dextrose
dfdsffsfdfsf
diatoms
diesel
Diesel Emissions Reduction Act (DERA)
diesel fuel blendstock
diesel prices
Diesel R5
diesel with renewables
diesel-range hydrocarbons
diesel-to-biodiesel conversion
diethyl ether
digital
Digital Biology
diisobutylene (DIB)
dilute acid hydrolysis pretreatment
DIN 51605
DIN EN 15376 (Ethanol blending component)
direct air capture
direct injection
direct ocean capture
Direct Sugar to Hydrocarbon Conversion (DSHC)
direct-to-fuel
directed evolution
dispense
distillates
distillation
distilled biodiesel
distilled palm methyl ester (DPME)
distilleries
distributed/centralized
distribution
distribution capacity
distribution waiver
diversification
divestment
DME/rDME (dimethyl ether)/renewable DME
DMF (2.5-dimethylfuran)
Dominican Republic
double cropping
drawdown
Drones/Unmanned Aerial Vehicles (UAV)
drop-in biofuels/hydrocarbons
drought
drought tolerant
drought-resistant
dry ice
dual cropping
dual-fuel/flex fuel ships
Dubai
duckweed
e
e-diesel
e-LNG (synthetic/electro Liquified Natural Gas)
e-methanol
e-NG (synthetic natural gas)
E. coli
E0
E0 price
E1
E10
E10 certification fuel
E10 price
E100
E100 conversion kit
E11
E12
E13
E15
E15 price
E15 pumps
E2
E20
E20 price
E20 pumps
E22
E25
E25 pumps
E27
E3
E30
E30 capable
E30 certification fuel
E30 optimized
E30 price
E30 pumps
E35
E4
E40
E40 conversion kit
E40 pumps
E5
E5 price
E50
E55
E6
E7
E70 diesel
E75
E78
E8
E80
E85
E85 conversion kit
E85 optimized engines
E85 price
E85 pumps
E90
E92
E95
E97
E98
earthquakes
East Africa
Eastern Europe
economic development
Economic Development Administration
economic modeling
economic policy
economics
Ecosystems Services
Ecuador
ED7 (7% ethanol 93% diesel)
ED95
education
Education Series 3030
educational business private
educational tour
EERE
efficiency
egg shell
Egypt
El Salvador
Electric aircraft
Electric Car/Electric Vehicle (EV)
electric car/Electric Vehicle (EV) Prices
electric grid
electricity
electricity price
electricity/power generation
electricity/power transmission
electrocatalysis
electrochemical
electrochemical cell
electrofuels (e-fuels)
electrofuels (e-fuels) prices
electrolysis
electrolytic cation exchange
electromethanogenesis (ME)
electrons
Elephant grass/Napier grass
elephants
embargo
eminent domain
emissions
emissions standards
EN 15751
EN 15940
EN 16709
EN 228
EN 590
EN228 (standard pump gasoline)
end user
end-of-life
Endangered Species Act (ESA)
Energy Bill
energy cane
energy consumption
energy crops
energy density
energy dominance
energy grasses
energy independence
Energy Independence and Security Act of 2007 (EISA)
Energy Information Administration (US EIA)
energy law
energy policy
energy prices
energy reserves
Energy Return on Energy Invested (EROEI or EROI)
energy security
Energy Security Trust
energy storage
enforcement
engine
Engine Development
engine problems
Engine/Fuel Co-optimization
engineering
England
enhanced oil recovery (EOR)
entrepreneur
environment
environmental impact study (EIS)
environmental justice/socially inclusive
environmental policy
Environmental Quality Incentive Program (EQIP)
Environmentalists
Enzymatic
enzymatic conversion
enzymatic depolymerization
enzymatic hydrolysis
enzyme production
enzyme recycling
Enzyme solicitation
enzymes
EPA (Environmental Protection Agency)
EPACT (Energy Policy Act)
Equatorial Guinea
equipment
eRINs/electric pathway
Eritrea
erosion control
EROWI (Energy Return on Water Invested)
ESG (Environmental Social Governance)
esterification
Estonia
ETBE (ethyl tert-butyl ether)
etha
ethane
ethanol
ethanol benefits
ethanol blend wall
ethanol blended diesel ED
ethanol blends/ethanol flex fuels
ethanol emissions
ethanol ether diesel fuel
ethanol fire
ethanol fuel cells
ethanol hybrid
ethanol pipeline
ethanol prices
ethanol production
ethanol pumps
ethanol tax
ethanol terminal
ethanol to gas
ethanol tolerance
ethanol-fueled aircraft
Ethanol-to-Gasoline (ETG)
ethanol/bioethanol
ethanol/diesel
ethanol/methanol synthesis
ethanol2G
Ethiopia
Ethiopian mustard
ethyl levulinate (EL)
ethylbenzene
ethylene
ets
eucalyptus
Euglena
European Emissions Trading System (ETS)
European Union (EU)
eutrophication
executive order
executive order--state
Extended Range Electric Vehicle (EREV)
externalities
extremophiles
f
F Factor
F-24
F-34
F-76 (Marine Diesel)
F-T
FAEE
FAEE (fatty acid ethyl esters)
Fair trade
False Claims Act
FAME (Fatty Acid Methyl Ester)
Farm Bill
Farm Bureau
farm equipment
farm policy
Farm to Fleet
Farm to Fly
farmers
farming
farnesane
farnesene
Fats
fecal sludge
Federal Aviation Administration (FAA)
Federal Bureau of Investigation (FBI)
Federal Emergency Management Agency (FEMA)
Federal Energy Regulatory Commission (FERC)
Federal Highway Administration (FHWA)
federal land
Federal Railroad Administration
Federal Reserve Bank
Federal Trade Commission (FTC)
Federal Transit Administration (FTA)
feed
Feed In Tariffs (FIT)
feed prices
Feedstock Flexibility Program for Bioenergy Producers
feedstock logistics
feedstock material
feedstock prices
feedstock storage
feedstock terminal
feedstock transportation
Feedstocks
fermentation
ferry
fertilizer
fiber
Fiji
Financing
Finland
Fischer-Tropsch Synthetic Kerosene with Aromatics (FT-SKA)
Fischer-Tropsch Synthetic Paraffinic Kerosene (FT-SPK)
Fischer-Tropsch Synthetic Paraffinic Kerosene with Aromatics (FT-SPK/A)
Fischer-Tropsch/FT
fish feed
fish oil
fish waste
fit for purpose
Fixed Base Operator (FBO)
flameleaf sumac
flavors
flax
fleet turnover
Fleets
fleshings
flex-fuel vehicles (FFV)
flight tests
Flightpath
flixweed/tansy/herb-Sophia
flood-prone soil
Florida
flue gas
FOG (Fats/Oils/Grease)
follow-the-crop
food
Food and Agriculture Organisation (FAO)
Food and Drug Administration (FDA)
food and fuel
food policy
food prices
food processing waste
food safety
food security
food vs biomaterials/bioplastics
food vs fuel
food waste
for
forage
forage sorghum
forecasts
foreign oil
Foreign Policy
forest
Forest Biomass for Energy
forest biotechnology
forest residue/waste
Forest resources
Forest Service
forestry
forklifts
Formate
formic acid
fossil carbon
fossil fuel
Frace
fracking
fractionation
fragrance
France
franchise
fraud
free fatty acids (FFA)
Freedom of Information Act (FOIA)
freight/cargo
French
French Guiana
fructose
fruit
FT-SKA
fuel
fuel additives
fuel cell electric vehicle (FCEV)
fuel cells
fuel economy
fuel efficiency
fuel injection
fuel mixtures
fuel molecules
fuel oil
fuel performance
fuel prices
Fuel Quality Directive (FQD)
fuel registration
Fuel Retailers
fuel testing
fuel transportation
fuel use
fuel wholesaler
fully burdened cost
fund
funding
fungus/fungi
Furanics
furfural
fusel oils
Future Farmers of America (FFA)
Gabon
gallium
Gambia
games
gas prices
gas tax/highway user fee
gas-to-liquid (GTL)
gasification
gasoline
gasoline baseline
gasoline consumption
gasoline mandate
gasoline markets
gasoline price
gasoline-range hydrocarbons
Gemany
General Services Administration
general waiver authority
generators
genetically engineered yeast cells
genetically enhanced microbes
genetically modified organism (GMO)
genome
Georgia
Georgia (country)
geothermal
German
Germany
Gerrmany
Ghana
GHG (Greenhouse Gas Emissions)
GHG (Greenhouse Gas Emissions) Intensity
giant cane
giant kelp
Giant King Grass
Giant Reed/Arundo
GIS
glass tubing
gliricidia sepium
global rebound effect
Global South
global warming
global warming potential
glucose
glycerin
glycerin standards
glycerol
goats
gorse
Governance practices)
Government Accountability Office (GAO)
government investment
government resources
government subsidies
grain sorghum/milo
grain speculators
grains
GRAND-AM
grants
grants-local
grants-state
grapefruit
grapes
graphene
graphite
GRAS (generally regarded as safe)
Grasses
grasshoppers
grease
Great Green Fleet
Great Lakes
Greece
green bonds
green chemistry
Green Deal EU
green economy
green house facility
Green Jobs
Green New Deal
Green Racing
Green Recovery
green/black economy
Greenland
GREET Greenhouse Gases Regulated Emissions and Energy Use in Transportation Model
Grenada
gribble
growers
gua beans
Guam
guar
Guatemala
Guava Seed
guayule
Guerbet reaction
Guinea
Guinea Bissau
Gulf states
gulmohar
Gumweed (grindelia squarosa)
Guyana
GWP
gypsum
h
Haiti
Halophytes
harvest site processing
harvesting
Hawai'i
hay
hazardous waste
hazelnut
HBIIP Higher Blends Infrastructure Incentive Program
HDCJ
HDO-SAK (hydro deoxygenated synthetic aromatic kerosene)
health
health benefits
health effects
heat of combustion
heat of vaporization
heat-tolerance
heather
heating oil/fuel
Heavy Duty Truck Rule
heavy duty vehicles (HDV)
hedging
HEFA (Hydro-processed esters and fatty acids)
HEFA50
helicopters
hemicellulace enzymes
hemicellulose
hemicellulosic sugars
Hemp
hemp oil
hemp seed
herb
hexanol
HFO (Heavy Residual Fuel Oil)
hibiscus
high blend renewable fuels (HBRF)
High Hydrogen Content Synthetic Paraffinic Kerosene (HHC-SPK)
High Octane Fuel (HOF)
High Octane Fuel Standard
High Octane Gasoline (HOG)
high octane low carbon (HOLC) fuel
High Octane Vehicles (HOV)
high performance regular
high school project
high sulphur fuel oil (HSFO)
high-octane/low-carbon (HOLC) liquid fuels
Highway Bill
highway rights-of-way
Highway Trust Fund
history
hog farmers
hombayniya
homogeneous-charge compression-ignition
Honduras
honey locust
Hong Kong
Honge tree nuts
hops
horticulture
Housing and Urban Development (HUD)
HPF (High Performance Fuels)
HRJ (Hydrotreated Renewable Jet)
human rights
Hungary
Hurricane Sandy
HVO (Hydrotreated vegetable oil)
HVO100
HVO20
HVO30
Hybrid aircraft
hybrid buses
hybrid locomotive
hybrid ships
hybrids
hydrocarbon fuels
Hydrocarbon-Hydroprocesed Esters and Fatty Acids (HC-HEFA-SPK)
hydrodeoxygenation
hydrodiesel
hydrofaction
hydroformylation
hydrogen aircraft
hydrogen carrier
hydrogen combustion engines
hydrogen fuel cells
hydrogen internal combustion engines
hydrogen leaks
hydrogen pipeline
hydrogen pumps/fueling stations
hydrogen tax credit
hydrogen terminal
Hydrogen/Renewable Hydrogen
Hydrogen/Renewable Hydrogen Price
hydrogenase
hydrogenation
hydrogenation-derived renewable diesel (HDRD)
hydrogenolysis
hydropower
Hydroprocessed fermented sugars to synthetic isoparaffins (HFS-SIP)
hydroprocessing
hydropyrolysis
hydrothermal carbonization
hydrothermal gasification
hydrothermal liquefaction (HTL)
hydrothermal treatment
Hydrotreated renewable diesel (HRD)
hydrotreating
hydrotreatment
hydrous ethanol
hypoxia zone
Iceland
Idaho
Illinois
Illiois
illuppai
ILUC (Indirect/Induced Land Use Change)
import/export
incinerator ash
India
Indian beech tree
Indian grass
Indiana
indirect effects
indirect emissions
indirect fuel use change
indium
Indonesia
industrial burners
industrial ethanol
industrial gases
industrial sugars
industrial waste
industrial waste gases
IndyCar
infographic
Infrastructure
inhibitors
innovation
insecticide/pesticide
insects
insurance
integrated biorefineries
integrated food/energy systems
intellectual property
Inter-American Development Bank
inter-crop
interactive map
intercropping
internal combustion engine (ICE)
internal combustion engine (ICE)/gasoline engine ban
International
international balance of payments
International Council on Clean Transportation (ICCT)
International Energy Agency (IEA)
International Maritime Organization (IMO)
International Monetary Fund (IMF)
International Organization for Standardization (ISO)
International Renewable Energy Agency (IRENA)
International Sustainability and Carbon Certification model(ISCC)
International Trade
International Trade Administration
International Trade Commission
Internships
inulin
invasive species
Investing
investment tax credit
Invvesting
ionic liquids
Iowa
IPCC Intergovernmental Panel on Climate Change
Iran
Iraq
Ireland
iridium
iron
iron oxide
IRS (Internal Revenue Service)
IS 1460
ISO 8217 (marine distillate fuel standard)
ISO 9000
isobutanol
isobutanol price
isobutanol pump price
isobutene
isobutylene
isomerisation
isooctane
isooctene
isopropanol
Israel
Italy
Ivory Coast
JAA
jackfruit
Jamaica
jamelão
Japan
jatobá
Jatropha
Jersey
Jerusalem artichoke
jet
jet A
Jet A-1
jet B
Jetfuel (Sustainable Aviation Fuel (SAF))
Jimmy Carter
Jobs
Joint Office of Energy and Transportation
jojoba
Jordan
JP-10
JP-4
JP-5/NATO F-44
JP-8/NATO F-34
juniper
Just A MInute
Just Transition
jute
K-12 Education
Kabakanjagala
kalanchoe
kamani
Kans grass
Kansas
Karanja
Kazakhstan
kelp
Kemiri Sunan
kenaf
Kentucky
Kenya
kerosene
ketones
kinggrass
Kiribati
knotweed
Knowledge Discovery Framework
Korea
Kosovo
kudzu
kukui nut
kulpa
kusum
Kuwait
Kygryzstan
labels
labor policy
Labrador
lactic acid
lactose
Lake County
lamp oil
land ownership
land prices
land rights
land subsidence
land tenure
land transfer
land use
land use change
land use policy
landfill methane
Landfills
landscape
Laos
Latin America
Latvia
LCFS (Low Carbon Fuel Standard)
lead
Leadtree
leaf ant
Lebanon
lecithin
legislation
Legislation-Federal
Legislation-State
lemna
lend-lease
Lesotho
lesquerella
leucaena
levulinic acid
Liberia
Libya
licensing
lichens
life cycle analysis (LCA)
light rail
lignin
Lignin Ethanol Oil (LEO)
Lignocellulosic Biofuel
lignocellulosic sugars
lime
Lipid
liquefaction
liquid
liquid petroleum gas (LPG)
liquid transportation fuels
liquidation
Liquified Biogas (LBG)
Liquified Biogas (LBG) pumps
liquified biomethane (LBM)
Liquified Natural Gas (LNG)
lithium
Lithuania
litigation
Litigation-Federal
Litigation-State
livestock
loan guarantees
loans
lobbying
loblolly pine
locomotives
lodgepole pine
logistics
long-term contracts
Louis
Louisiana
low c
low carbon emissions
low carbon octane standard (LCOS)
Low Emission Vehicle Standards (LEV)
low sulfur diesel
low sulfur fuel
low sulfur marine fuel
LSMGO (Low Sulfur Marine Gas Oil)
lubricants
lumber mill
Luxembourg
lysis
M100
M15
M3
M50
ma
macadamia
macauba
Macedonia
machine learning
machinery
macororo
Madagascar
magnesium
mahua
Maine
Malawi
Malaysia
Maldives
Mali
mallees
Malta
Malyasia
mamona
management changes
mandates
mangaba
manganese
mango
mangrove
Manitoba
mannose
manure
maple
maps
marginal land
marine algae
Marine Corps
Marine Diesel Oil (MDO)
Marine Fuel Oil
Marine Gas Oil (MGO)
Marine/Maritime Bio and Renewable/Sustainable Fuel (SMF)
Marine/Maritime Bio and Renewable/Sustainable Fuel (SMF) price
Marine/Maritime Bio and Renewable/Sustainable Fuel Terminal
Marine/maritime renewable fuel terminal/bunkering
market forces
market share
marketing
markets/sales
Mars
Marshall Islands
Maryland
Masdar Institute
mass balance standard
Massachusetts
Master Limited Partnership (MLP)
Mauritania
Mauritius
Mazda
meat
mechanics training
medical waste
MEEC
membranes
mergers and acquisitions
mesquite
methanation
methane leaks
methane/biomethane
methanization
methanol benefits
methanol fuel cells
methanol hybrid
methanol price
Methanol-to-Gasoline
Methanol-to-Jet (MTJ-SPK)
Methanol/Biomethanol/Renewable Methanol
methylbutenol
Mexico
Michelin GreenX Challenge
Michigan
micro-crop
microalgae
microbial electrosynthesis
microbiology
microorganisms/microbes
microwave
Mid-Atlantic
Middle East
Midwest
mileage
military
military policy
military reserves
military specifications
military strategic flexibility
military strategy
military use of biofuels
milk permeate
millennium fruit
millet
millettia pinnata
milo stover
mineralization
minerals
mining
Minn
Minnesota
miscanthus
misfueling
missile fuel
Mississippi
Missouri
mixed prarie
mobile refinery
modeling
modular
molasses
mold
Moldova
molinia
molybdenum
MON (Motor Octane Number)
Monaco
Mongolia
mongongo
monitoring/measuring reporting verifiction (MRV)
Montana
Montenegro
moose
morama
Moringa tree
Morocco
morula
motorcycles
motors
MOVES (motor vehicle emissions simulator) modeling system
MOVES2014
MOVES3 (MOtor Vehicle Emission Simulator model)
Mozambique
MSW (Municipal Solid Waste)
MTBE (Methyl tert-butyl ether)
multi-fuel
municipal/city
mushroom
mushroom substrate
mustard seed
mvr
Myanmar
n-butanol
n-butene
nahar
Namibia
nano
nano particles
nanocatalysts
nanocellulose
nanomaterials
naphtha/bionaphtha/renewable naphtha
naphthene
NASCAR
National Academies of Science
National Aeronautics and Space Administration (NASA)
National Energy Council
National Environmental Policy Act
National Guard
National Highway Traffic Safety Administration (NHTSA)
National Institute of Standards and Technology (NIST)
National Institutes of Health (NIH)
National Laboratory
National Oceanic and Atmospheric Administration (NOAA)
National Oilheat Research Alliance
National Park Service
National Research Council
National Science Foundation (NSF)
national security
National Security Council
National Transportation Safety Board
National Transportation Safety Board (NTSB)
Nationally Determined Contribution (NDC)
Native American/American Indian/First Nation Tribes
natural gas
Natural Gas Act
natural gas input
natural gas prices
natural gas vehicles
natural gasoline
Navy
Nebraska
neem
negative carbon emissions
NEN 7427-1
neodymium
Nepal
net energy balance
Netherlands
Nevada
New Brunswick
new fuel approval
New Guinea
New Hampshire
New Jersey
New Mexico
New South Wales
New York
New Zealand
Newfoundland
Newfoundland and Labrador
next generation biofuels
next generation vehicles
NHRA drag racing
Nicaragua
nickel
Niger
Nigeria
nipa sap
nitrate leaching
nitrates
nitrogen
Nitrogen fertiliser
nitrogen starvation
nitrous oxide (N2O)
Niue
NO2
noodles
nopal
North Africa
North America
North Carolina
North Dakota
North Korea
Northeast
northern catalpa
Northern Ireland
Northern Territory
Northwest Territories
Norwary
Norway
Nova Scotia
NOx (nitrogen oxides)
noxious weeds
nuclear
Nunavut
nut shells
nutraceuticals
nutrient credit trading
nutrient management
nutrients
nutrition
oak
oat hulls
oat straw
oats
Obligated Parties/Point of Obligation (PoO)
ocean-based energy
Oceania
octane
octane price/value
octanol
Office of Energy Efficiency and Renewable Energy
Office of Management and Budget (OMB)
Office of Science and Technology Policy
Office of Science and Technology Policy (OSTP)
Office of Science Technology and Policy (OSTP)
Offices of Inspector Generals
offtake agreements
Ohio
oil
oil embargo
oil exploration
oil monopoly
oil p
oil price parity
oil prices
oil production
oil refineries
oil replacement
oil sands
oil seed
oil seed crops
oil speculators
oil spill
oil subsidies
oil taxes
oil/gas terminals
Oilcane
Oils
Oklahoma
olefins
oligomerization
olive cake
olive oil
olive pits
olive pomace
olive water
olives
Oman
Omega-3s
on-farm algae production
on-farm ammonia production
on-farm biodiesel
on-farm ethanol production
on-farm natural gas production
on-farm processing
on-site hydrogen production
one p
one pound waiver
onion waste
online courses
Ontaio
Ontario
OPEC (Organization of the Petroleum Exporting Countries)
open fuel standard
open pond
opportunity zones
optimized flex fuel vehicles
orange peel
orchard grass
orchard prunings
Oregon
organic solar cells
Organization for Economic Cooperation and Development (OECD)
osage orange
OSHA
Overseas Private Investment Corporation
overview
overview/survey course
owa
oxygen
oxygenate
ozone
Pakistan
Palau
palm
palm biomass
palm fatty acid distillate
palm fiber
palm fronds
palm kernel
palm kernel oil
palm kernel shell
palm oil
Palm Oil Methyl Ester (PME)
palm oil mill effluent (POME)
palm oil prices
palm trunk sap
palm waste
Paludiculture/peatland cultivation
Panama
pandas
panic grass
papaya
paper
Papua Indonesia
Papua New Guinea
paraffins
Paraguay
Paris Agreement
parity
partial waiver
particulates
pasture land
Patent and Trademark Office (PTO)
patents
pathways
Paulownia
paulownia tree
payments
peach shell
peaches
peak oil
peak oil demand
peanuts/groundnuts
peas
pectin
peela kaner
pellet
pellets
Pennsylvania
pennycress/stinkweed
pentane
pentanol
pentose
pequi
perennial grains
perennial grasses
Performance
permitting
Peru
pest-tolerance
pesticide-tolerance
pests
pet food
petition
petroleum
pharmaceuticals
phase separation
Philippines
phosphorus
photobioreactor
photoelectrocatalysis
photoelectrochemical
photolysis
photosynthesis
phragmites
pigeon pea
pilot
pilot scale
pine
pine beetle
pine needles
pine nut
pineapple
Pineapple leaf
pinion
Pipeline and Hazardous Materials Safety Admin (PHMSA)
pipelines
Pistacia chinensis
PLA
plant cell research
plant cell walls
plant oil
plastic
plastic-to-jet
platinum
Plug-in Flex Fuel Hybrid
Plug-in Hybrid Electric Vehicle (PHEV)
plume grass
Poand
podcasts
Poland
poli
Policy
politics
pollinators
pollution
pollution control
polyethylene
polyfuel
polymer
polymerization
polysaccharides
pomace
pomegranates
pongamia
pongamia pinnata
poplar
poppy
population control
Portable refinery
Portugal
poster sessions
potamogeton
potassium
potato
poultry litter/waste
power
power-to-x/gas/liquid
prairie grasses
pre-processing
precision farming/agriculture
precursors/biointermediates
premium gasoline
Pretreatment
pretreatment equipment
price
price of water
prickly pear
Prince Edward Island
process flow diagram
producer tax credit
Production tax credit
productivity
project insurance
propagating
Propane/Biopropane/Renewable Propane
propane/renewable propane pumps
propanol
property insurance
propylene
protectionism
protein
protests
proton exchange membrane (PEM)
public comments
public health policy
Puerto Rico
pulp
Pulp/Paper Mill
pump retrofit kit
pumps/fueling station
pungam
Punnai tree
pyrolysis
pyrolytic liquefaction
Q-RIN
QAP
Qatar
quality assurance
Quality Assurance Plans (QAPs)
quality improvement
quantum dots
Quebec
Queensland
quote of the week
r
R Factor
R100/RD100
R33
R5
R95B5/RD95B5
R99/RD99
rabbits
race
radiata pine
radish leaves
Rahal Letterman Lanigan Racing
railroad
rain tree
rainforest
ranchers
RAND
rare earth metal/critical minerals
RD10
RD100
RD20
RD3
RD30
RD40
RD50
RD55
RD80
RD80B20
RD99
reclaimed mine lands
Recycled Carbon Fuel (RCF)
recycled oil
recycled plastics
recycling
red algae
redcedar
Reducing Emissions from Deforestation and Forest Degradation
Refined Bleached Deodorized Palm Oil (RBDPO)
refineries
reforestation
Reformate
regenerative braking
regenerative farming
Regional Conservation Partnership Program (RCPP)
Regulated Emissions
regulations
Regulations-Federal
Regulations-State
Regulatory Enhancement Growth Support (REGS)
Reid vapor pressure (RVP)
remediation
remediation rice straw
Renewable Chemical
renewable chemical producer tax incentive
renewable chemical production tax credit
renewable diesel pipelines
Renewable Diesel Production
renewable diesel pumps
renewable diesel tax credit
renewable diesel terminal
Renewable Diesel/Green Diesel price
Renewable Diesel/Green Diesel/HVO/Paraffinic Diesel
Renewable Energy
Renewable Energy Directive (RED/RED II/RED III)
Renewable Energy Standard
Renewable Energy to Fuels through Utilization of Energy-Dense Liquids (REFUEL)
renewable fuel
renewable fuel oil (RFO)
Renewable Fuel Standard (RFS and RFS2)
Renewable Fuel Standard (RFS2) revisions/repeal
Renewable Fuels Directive (EU)
renewable fuels of non-biological origin (RFNBO)
renewable gasoline blendstock
renewable marine diesel
renewable naphtha-with-ethanol-t0-jet (NETJ)
Renewable Natural Gas (RNG)
Renewable Natural Gas (RNG) price
Renewable Natural Gas (RNG) pumps
Renewable Portfolio Standards
Renewable Power Standard
Renewable Synthesized Iso-Paraffinic Fuels (SIP)
Renewable Transport Fuel Obligation (RTFO)
renewable volume obligation (RVO)
REnova
RenovaBio
replacement molecules
Repowering Assistance Program
Republic of Congo
repurpose
research and development
research facility
resiliency
resource depletion
resurrection grass
retail
retrofit
return on investment
Reverse Water-gas Shift
RFI (Request for Information)
RFS "reset"
RHD100
Rhizosphere Observations Optimizing Terrestrial Sequestration (ROOTS)
Rhode Island
rhododendron
Ricardo
rice
rice bran
rice bran oil
rice hulls
rice husks
rice price
rice straw/paddy straw
RICO (Racketeer Influenced and Corrupt Organizations Act)
RIMPAC
RINs (Renewable Identification Numbers)
RINs markets
RINs price
risk management
RJ-4
RJ-6
RME (rape methyl ester)
RME180
RNA (Ribonucleic acid)
RNG tax credit
roadmap
rocket fuel
Romania
RON (Research Octane Number)
rosin
rotation crops
Roundtable on Sustainable Biomaterials (RSB)
royalties
RP-1
RTP (rapid thermal processing)
rubber
rubber seeds
rumen
ruminants
rural development
Rural Energy for America Program (REAP)
Rural Energy Self-Sufficiency Initiative
Rural Renewable Energy Pilot Program
rushes
Russia
Russian olive
rutabaga
Rwanda
ry
rye
Rye grass
rye straw
s
saccharification
SAF pipeline
SAF10
SAF30
SAF40
SAFc (Sustainable Aviation Fuel certificates)
Safer and Affordable Fuel Efficient Vehicles (SAFE)
safety
safflower
sago pond weed
SAIC
sal tree
Salicornia
salt water
salt-tolerant
saltbush
saltcedar
Samoa
Sanctions
Santa Monica
sardine oil
Saskatchewan
Saudi Arabia
sawdust
scale up
Scandinavia
scholarships/fellowships
Science Advisory Board (SAB)
Science Based Targets initiative (SBTi)
Science Policy
scooters
Scotland
scum
sea level rise
seaports
seashore mallow
seawater
seaweed cultivation
Seaweed/Macroalgae
second-generation biofuel income tax credit
Section 526
Securities and Exchange Commission (SEC)
seed husks
seed-to-wheel
Senegal
Serbia
sesame
sewage
Seychelles
shale
shale gas
shale oil
shark oil
Shea
sheep
shellfish
shipping
shipping containers
shipworm
siam weed
Sierra Leone
silage
silica
Silphie/cup plant/Indian cup
silver
silver maple
simarouba
Singapore
Singpore
sisal
SK
slash
Slovakia
Slovakia/Slovak Republic
Slovenia
sludge
Small Business Administration
Small Business Innovatin Research (SBIR)
Small Business Technology Transfer (STTR) Program
small engines
small refinery exemption (SRE)
smog
smokestack
soap
soapstock
Social
social benefit investing
social cost
social value
social venture
Society of Automotive Engineers (SAE)
soi
soil
soil amendments
soil carbon
soil health
soil microbial biomass
solar energy
solar energy-to-chemical conversion
solar fuel
solar thermochemical hydrogen (STCH)
solaris
Solid Oxide Electrolyzer Cell (SOEC)
solid oxide fuel cell (SOFC)
Solomon Islands
Solutions
solvent liquefaction
Somalia
soot
sorghum
sorghum oil
sorghum price
sorghum stover
South Africa
South America
South Australia
South Carolina
South Dakota
South Korea
South Pacific
South Sudan
Southeast Asia
Southern Africa
Soviet Union
SOx (Sulfur oxides)
soy meal
soybean hulls
soybean prices
soybeans
Spain
spartina
specifications
Spekboom
Spent Bleaching Earth Oil (SBEO)
sprawl
spruce
Sri Lanka
Stakeholders
standards
start-up
State Department
Statistics
steam explosion
steam methane reformation
steam reformation
steel
stevia
stillage
storage tanks
Straight (pure) Vegetable Oil (SVO or PVO)
stranded assets
Strategic Bioenergy Reserve
STrategiv Petroleum Reserve
straw
students
su
sub-Saharan Africa
sub-sim (substantially similar)
succinic acid
sucrose
Sudan
sugar
Sugar Beets/Energy Beets
Sugar kelp
sugar palm
sugar platform
sugar prices
sugar standards
sugar-to-biodiesel
sugar-to-farnesane
sugar-to-jetfuel
sugarcane
sugarcane prices
sugarcane straw
sugars
sugars-to-fats
sulfur
Sumatra
sunflower
sunflower stalks
supercritical fluid
supercritical hydrolysis
supply agreements
supply chain
Supreme Court
surahart
Surface Transportation Board
Suriname
Sustainability
Swaziland
Sweden
sweet potatoes
Sweet sorghum
sweetgum
swine waste
Switchgrass
Switzerland
sycamore
syngas (synthesis gas)
syngas/gas fermentation
SYNHH
synthesised aromatic kerosene (SAK)
synthetic biology
synthetic diesel
synthetic gasoline
synthetic kerosene
synthetic liquified gas (SLG)
synthetic methane/e-methane
synthetic natural gas
Syria
Tailoring Rule
Taiwan
Tajikistan
tall fescue
tall oil
tallow
tallow tree
tamanu/nyamplung
Tamarix
tank cars
tank-to-wheel
tanker trucks
tankers
Tanzania
tar sands
tariffs
taro
Tasmania
tax benefit
tax credits
tax incentives
tax parity
tax policy
taxes
tea
teach
teach-the-teacher
teacher
teacher resources
teacher training
tech transfer
technical course
Technical Readiness Levels
techno-economic analysis
technology transfer
telephone utility poles
Tennessee
termites
terpenes
terrestrial carbon
testing
Texas
textbook
Thailand
theft
therapeutics
Thermal catalytic depolymerization (TCD)
thermal deoxygenation
thermocatalytic conversion
thermochemical conversion
thermochemical liquefaction
Tibet
Tier 3
Tier 4
tilapia
tillage
Timor-Leste
tires
tobacco
tobacco tree
Togo
Tokyo
toluene
Tonga
tool
Toronto
torrefaction
totai
Toxic Substances Control Act (TSCA)
trade
trade dispute/discrimination
trade group
trade organization
Trade Policy
trade secrets
training
trains
transesterification
transgenics
transition
Transportation Fuels Policy
Transportation Fuels Policy--Municipal
Transportation Fuels Policy--State
Transportation Policy
travel policy
Treasury Department
trees
Trinidad and Tobago
triticale
trucks
tubers
tugboats
tung
tunicate
Tunisia
Tunsia
Turkey
U.S. Trade Representative (USTR)
UCOME (Used Cooking Oil Methyl Ester)
Uganda
UK (United Kingdom)
UK Emission Trade Scheme (UK ETS)
Ukraine
Ukriane
UL (Underwriters Laboratory)
ULSD (ultra low sulfur diesel)
Ultra Low Sulfur Fuel Oil (ULSFO)
Ultra-low-carbon bioethanol
underground storage tanks (UST)
UNESCO
UNIDO (United National Industrial Development Organization)
United Arab Emirates (UAE)
United Nations (UN)
United Nations' International Civil Aviation Organization (ICAO)
United Nations' Sustainable Development Goals (SDG)
United States Auto Club
Unleaded 88/E15
uranium
urban sprawl
urbanization
Uruguay
US Agency for International Development (USAID)
US Army
US ethanol exports
US Geological Survey
US Product Safety Commission
USAC
USAID
USDA Agricultural Research Service (ARS)
used cooking oil (UCO)
used motor oil
used railroad ties
ustain
Utah
utilities
utility model
Uzbekistan
value chain
Value Stack
vanadium
Vancouver
Vanuatu
Vatican
VEETC (volumetric ethanol excise tax credit)
vegetable oils
vehicles miles traveled (VMT)
Velocys
Venezuela
Vermont
vetiver
Victoria
video
Vietnam
vinasse
vinegar
vineyard waste
Virgin Islands.
virgin oils
Virginia
viruses
vlsfo
VLSFO (very low sulfur fuel oil)
volatile fatty acids (VFA)
volunteers
VTOL (vertical take-off and landing aircraft)
Vulcanol
w
waiver
Wales
warranty
Washington
Washington DC
waste
waste alcohol
Waste CO2
waste heat
waste management
waste oil
waste paper
waste vegetable oil
waste-to-chemicals
Waste-to-Energy
waste-to-fuel
wastewater
water
water consumption
water footprint
water hyacinth
water policy
water pollution
water quality
water treatment
water vapor
watermeal
watermelon
wax
weather
well-to-wheel
West Africa
West Coast
West Java
West Virginia
Western Australia
wet distillers grain
wet extraction
What You Can Do
wheat
wheat bran
wheat fiber
wheat prices
wheat straw
wheatgrass
whey
whisky
white grease
White House
wildlife habitat
willow
wind energy
wine wastage/grape marc
winter crops
Wisconsin
Wisdonsin
women
Wood
woody biomass
World Bank
World Trade Organization (WTO)
Wyoming
XTL
xylan
xylene
xylose
yard waste
yeast
yellow grease
yellowhorn tree
Yemen
Yields
Yukon
Zambia
Zanzibar
zein
zeolites
zero-carbon bioethanol
Zimbabwe
zinc
zoning
© 2008-2023 Copyright Advanced BioFuels USA. All Rights reserved.
0 COMMENTS
Leave A Comment
Your Email Address wiil not be Published. Required Field Are marked*